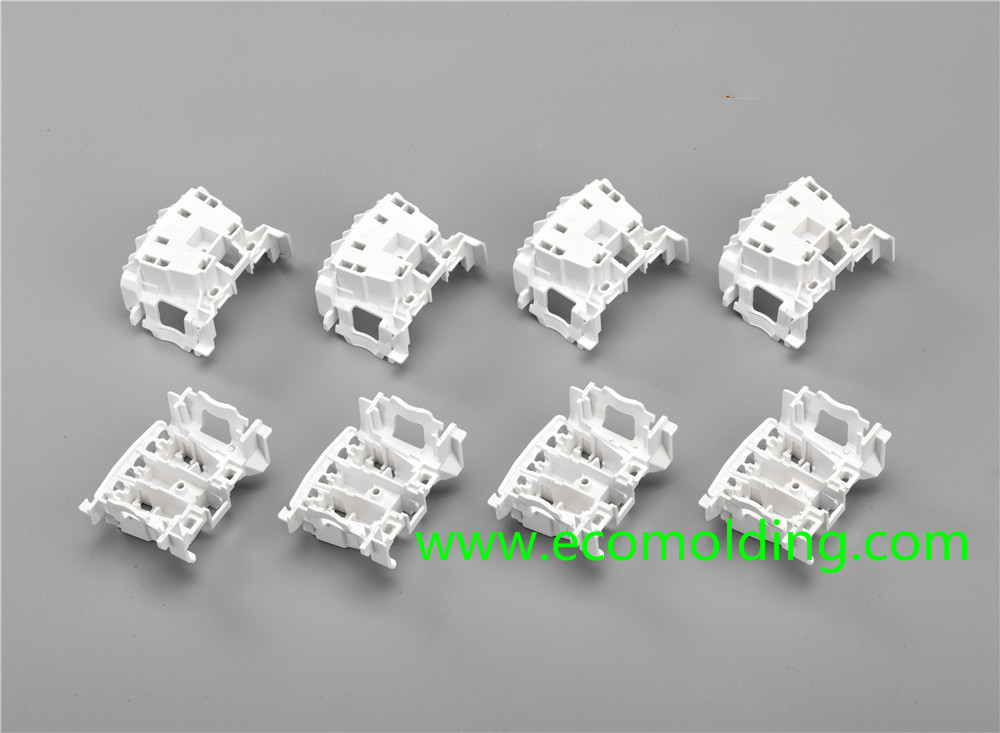
Plastic annealing process
The purpose of plastic annealing is to eliminate internal stress. For example, in the area where the thin and thick parts meet, the cooling of the thick part is slower than that of the thin part, causing the joint to shrink unevenly. As a result, there is stress concentration in the area. This phenomenon is more obvious around metal inserts. If annealing is not performed, cracking or even deformation may occur in the stress concentration area after a period of time. Annealing method: Usually, the product is immersed in hot oil, hot water, or cycling hot air. The annealing temperature is adjusted according to the type of the plastic, but usually, it is 10-20°C lower than the product’s thermal deformation temperature, or the product will deform. However, the temperature should not be too low either, or the desired effect will not be achieved.
Annealing conditions for several common plastics are shown in the table below:
Plastic | Agent | Temperature (°C) | Product Thickness (mm) |
Time (min) |
Nylon | Oil | 130 | 12 | 15 |
ABS | 80-100 | 16-20 | ||
PC | Air | 125-130 | 1 | 30-40 |
PE | Water | 100 | >6 | 60 |
PP | Air | 150 | <6 | 15-30 |
PS | Air or Water | 60-70 | <6 | 30-60 |
PSU | Air or Water | 160 | <6 | 60-180 |
Moisture Conditioning of Plastic Products
Moisture conditioning of plastic products is mainly for polyamide (nylon) products. After storage for a period of time, products made from this raw material will deform and expand due to absorption of moisture in the air, thus resulting in size change. Therefore, after a nylon product is molded, it should first be immersed in 100-120°C water or potassium acetate solution, to keep it isolated from the air. The immersion time is determined according to the wall thickness and the shape of the product. Then, take the product out after the temperature is slowly lowered to the room temperature.