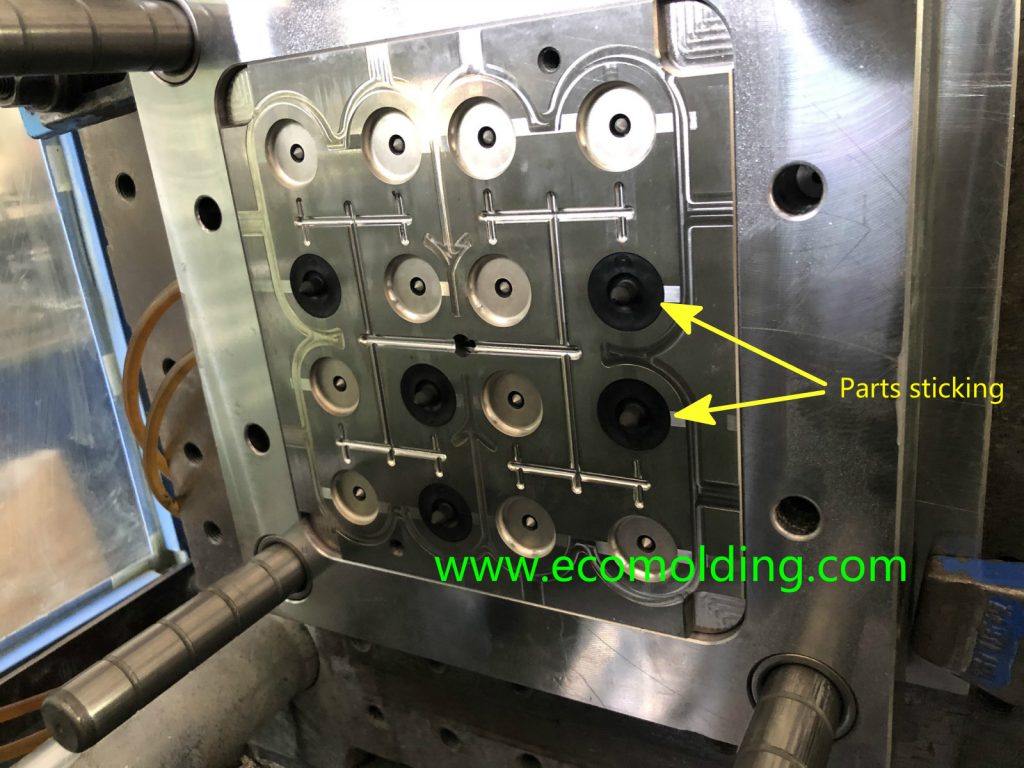
The causes of parts sticking and sprue sticking are multifaceted, among which mold failure is one of the main reasons. The reasons and corresponding solutions are described as follows:
1. The surface of the mold cavity and sprue bush is rough. If there are surface defects such as gouges, nicks, scars, and dents in the mold cavity and sprue bush, the plastic parts and sprue will easily stick to the mold, resulting in difficulty in ejection. Therefore, the surface finish of the cavity and sprue should be improved as much as possible. The inner surface of the cavity should preferably be chrome-plated. When polishing, the movement direction of the polishing tool should be the same as the direction of mold filling.
2. The mold wears, is scratched or the insert clearance is too large. When the molten material produces flashing in the scratched part of the mold or in the clearances between the inserts, it can also cause difficulty in product ejection. In response, the damaged mold area should be repaired and the clearances between the inserts reduced.
3. The mold rigidity is insufficient. If the mold cannot be opened at the beginning of injection, it means that the mold is deformed under injection pressure due to the insufficient rigidity. If the deformation exceeds the elastic limit, the mold cannot return to its original state and thus cannot be used anymore. Even though the deformation does not exceed the elastic limit of the mold, the molten material is cooled and solidified under high conditions in the mold cavity. After the injection pressure is removed and the mold recovers from deformation, the plastic part is clamped by the rebound force, so the mold still cannot be opened.
As a result, when designing the mold, sufficient rigidity and strength must be ensured. When trying the mold, it is the best to install a dial indicator on the mold to check whether the mold cavity and the mold base are deformed during the filling process. During mold trial, the initial injection pressure should not be too high. You should observe the deformation, while slowly increasing the injection pressure, so as to keep the amount of deformation within a certain range.
When mold clamping failure occurs due to the too-high rebound force, it is not enough to increase the mold opening force alone. But instead, the mold should be disassembled immediately, and the plastic part should be heated and softened before being taken out. For molds with insufficient rigidity, a frame can be mounted on the outside of the mold to increase its rigidity.
4. The draft angle is not big enough, or the parallelism between the core and cavity plates is poor. When designing and making the mold, a sufficient draft angle should be ensured, otherwise it will be difficult to eject the plastic product. Forceful ejection often causes the plastic part to warp, leading to ejection marks or cracks. The core and cavity plates of the mold must be relatively parallel, or it will cause the cavity to deviate, thus resulting in parts sticking.
5. The design of the gating system is inappropriate. Part sticking and sprue sticking will be caused, when the runner is too long and too small in size, the connection between the main runner and the branch runner is not strong enough, there is no cold slug well in the main runner, the gate is poorly balanced, the diameters of the main runner and the nozzle are not properly matched, or the gate sleeve and the spherical nozzle surface do not match. Therefore, the length and the cross-sectional area of the runner should be appropriately reduced, and the connecting strength between the main runner and the branch runner increased, with a cold slug well provided in the main runner.
When determining the gate location, the filling rate of each cavity in a multi-cavity mold should be balanced and the pressure in each cavity reduced by adding auxiliary gates. In general, the diameter of the small end of the main runner should be 0.5-1mm larger than the nozzle diameter, and the concave radius of the gate sleeve should be 1-2mm larger than the nozzle radius.
6. The ejection mechanism is not appropriately designed or operated. If insufficient stroke, uneven ejection or poor ejector plate movement occurs to the ejection mechanism, the plastic parts will not be able to be ejected.
When the conditions allow, the effective ejection area should be increased as much as possible to ensure a sufficient ejection stroke. The ejection speed of the plastic part should be kept within a suitable range, neither too fast nor too slow. The main reason for the undesired movement of the ejector plate is the stickiness between the sliders.