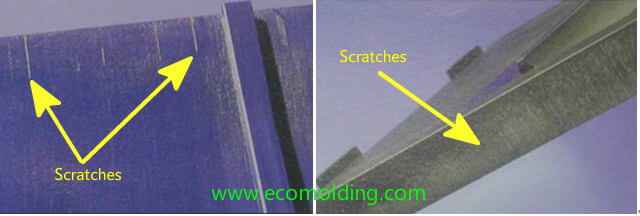
The scratches (scrape marks)on the appearance of an injection molded product usually occur on such deep-cavity products as chargers, routers, and chassis, etc. It is also a particularly common problem during the injection molding process, known as one of the 10 most challenging problems in the mold and injection molding industry. Glossy products, as well as products with textured sides are easily scratched. What on earth has caused it? When it comes to the scratches on the textured surface, the first thing that comes to the mind of an engineer is that the draft angle on the side of the product is not large enough, but why the scratch still exist after the draft angle is increased? So, solving the occurrence of scratches is not just a matter of the draft angle. In fact, it is not so simple at all. Now, let’s thoroughly analyze and solve the problem of surface scratches.
The causes of surface scratches mainly include the following factors:
I. Draft Angle
The key issue with the product is that the draft angle of the product is too small, resulting in scratches on the side of the product. To respond to the different texture requirements on the side of the product, we have already gained relevant experience – apply suitable draft angles for texture surfaces of different specifications. To solve this problem, we must try to avoid it in the early stage of product evaluation. If the customer’s product does not allow a sufficient draft angle, we must consider using other mold mechanisms or other technical means to avoid it.
II. Mold Design
In addition to problems with the product, to avoid scratches, mold design also plays a very important role, so you must consider it carefully. Here are some examples to explain how to avoid product side scratches through mold design.
1.To handle the fillet of the parting surface, product designers often directly put in the fillet when designing the product. In fact, this is an unreasonable design, because the draft angle at the conjunction between the fillet and the surface is close to zero, which is easy to cause scratches.
2. Mold Structure: Improper mold matching design will also cause the core and the cavity to be misaligned during the mold opening process, thus causing product scratches.
3. When designing the mold gate, you should consider the gate design so as not to cause too much pressure on the product and cause side scratches on the product. The gate should be as far away as possible from the textured side surface, because the pressure at the gate is high also with a long pressure holding time, so the high clamping force will make the product to be prone to scratches.
4. The product sticks to the mold cavity: We must ensure that the product 100% sticks to the mold core when the mold is open. If it sticks to the mold cavity, local product warpage may be caused, and thus scratches on the side surface. When necessary, a product fixing structure must be deployed in the mold core to ensure that the product stays with the core.
III. Mold Machining
1. Although the draft angle is designed to be big enough, it is easy to cause errors during mold machining, because it is difficult to measure the angle accurately. This point must be taken into consideration.
2. It is the easiest to create undercut on the side wall of the mold cavity during mold polishing, because the mold polishers are often afraid to polish the parting surface into a fillet. The mold polishing workload close to the bottom is higher and the one close to the parting surface is lower, which is nothing less than reducing the draft angle of the product, so it is also a possible factor that causes product scratches.
IV. Molding Machine Adjustment
1. Excessive injection pressure and holding pressure are also important causes of scratches on product side walls. Excessive injection pressure creates stress that causes product warpage in the mold. The product may be locally pressed on the side wall, so it is easy to scratch the product side surface during mold ejection.
2. Excessive material temperature will also cause the product surface to be easily scratched.
3. Insufficient product cooling is also one of the causes of product scratches.
4. The bulging of the parting surface also easily causes product scratches. The parting surface bulging caused by excessive clamping pressure, too-soft mold material, and resin powder, etc. may also cause the product side surface to be scratched, so the mold parting surface and texture surface must be kept clean.
5. The injection molding machine is aging, so the parallelism between the front and rear plates is poor. The vibration during mold opening may also be one of the factors that cause scratches on the product side surface.
All in all, the main factors that cause scratches on the side wall and textured surface of a product are comprehensively considered above. Only by carefully following the steps one by one can we avoid the troublesome scratches on plastic injection molded products.